Manutenzione correttiva, preventiva e predittiva: un focus sulle politiche di manutenzione
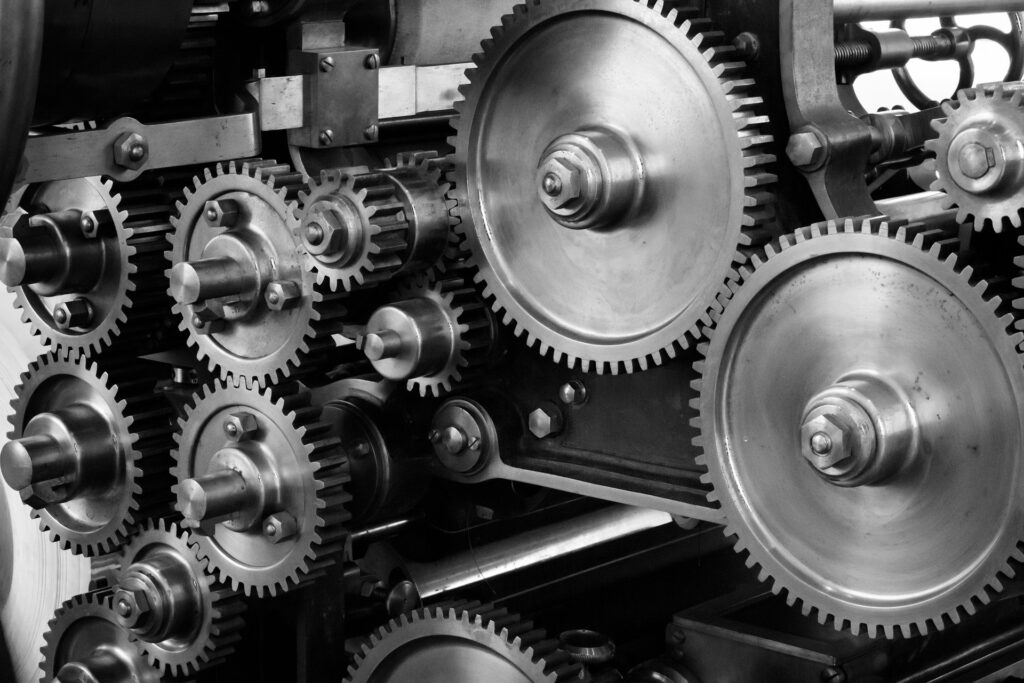
Manutenzione correttiva, preventiva o predittiva? Ma che vuol dire? Che cosa sono le politiche di manutenzione? Vediamo insieme le varie politiche di manutenzione, i loro vantaggi e svantaggi e quale di esse può adattarsi meglio al singolo caso…
Cosa troverai in questo articolo:
Il mondo della manutenzione: breve storia
Prima metà del secolo scorso
Storicamente la manutenzione nasce come manutenzione correttiva nella produzione artigianale, salvo alcune forme elementari di prevenzione. In parole semplici: quando un macchinario si rompeva veniva aggiustato. Solamente agli inizi del ‘900, con la nascita della produzione di massa e i conseguenti criteri standard e gli alti volumi produttivi, si palesano necessità di continuità e qualità nei sistemi di produzione. Dall’inizio dello scorso secolo, dunque, si iniziano a sviluppare le prime forme di manutenzione preventiva di tipo ciclico. In parole semplici, si iniziarono a sostituire periodicamente i componenti più soggetti ad usura. A partire dagli anni ’40, inoltre, si implementano anche metodi per la logistica di supporto alla manutenzione.
Seconda metà del secolo scorso
Negli anni ’60, con la crescente complessità dei sistemi, i soli metodi di prevenzione ciclica si rivelano inadeguati e troppo costosi. Nasce, dunque, l’approccio di manutenzione secondo condizione e predittiva grazie all’introduzione di svariate tecniche di diagnostica. Sono degli anni ’70, invece, le tecniche produttive giapponesi che introducono forti cambiamenti con i concetti di Just In Time (JIT), Total Quality, Continuous improvement, manutenzione produttiva e quant’altro, fino ad arrivare alle soluzioni di automanutenzione, integrazione manutenzione-produzione, miglioramento continuo e manutenzione predittiva secondo condizione. Vediamo insieme le tre principali politiche di manutenzione che è possibile adottare in un sistema produttivo…
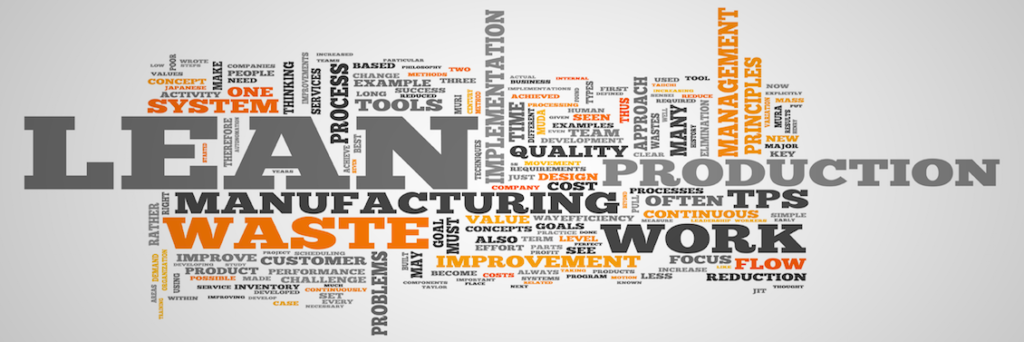
1. Manutenzione correttiva
La manutenzione correttiva consiste nel mantenere il componente/sistema in funzionamento fino a che il manifestarsi del guasto non imponga l’arresto del sistema. L’intervento di manutenzione ha l’obbiettivo di riparare e ripristinare le condizioni iniziali nel minor tempo possibile. In pratica, il componente/sistema è in funzione fino a quando qualcosa non si rompe, solo in seguito al guasto si interviene e si ripara il guasto nel minor tempo possibile.
Manutenzione correttiva: vantaggi e svantaggi
Indubbiamente il vantaggio maggiore della manutenzione correttiva è che consente di contenere i costi propri di manutenzione: infatti, fin quando l’entità funziona, il costo variabile è nullo. Tra gli svantaggi rileviamo immediatamente che guasti accidentali potrebbero portare a possibili situazioni di rischio per la sicurezza, interruzione improvvisa del servizio e una possibile riduzione della qualità del prodotto/servizio. Altri svantaggi notevoli sono l’utilizzo molto variabile delle risorse fisse (squadre di manutenzione) e una tendenza al sovradimensionamento del magazzino ricambi.
2. Manutenzione preventiva
La manutenzione preventiva (o ciclica) consiste nella sostituzione programmata di un determinato componente non ancora giunto a rottura. In questo modo si cerca di prevenire il cedimento accidentale migliorando l’affidabilità del sistema. Il programma di attività preventive è concordato dalle funzioni esercizio e manutenzione tenendo conto delle rispettive esigenze. Nella manutenzione preventiva è fondamentale definire preventivamente gli intervalli tra un intervento e il successivo, pertanto nasce il bisogno di creare uno storico dei guasti delle macchine per ottenere statistiche da abbinare alle indicazioni del costruttore.
Manutenzione preventiva: vantaggi e svantaggi
In questo caso i vantaggi sono molteplici: ad esempio, si possono limitare le perdite di funzionalità a seguito di guasti accidentali in entità critiche, si può programmare meglio l’utilizzo degli operatori di manutenzione, ottimizzare le scorte dei ricambi e ridurre i tempi di fermo impianto. D’altro canto, la manutenzione preventiva potrebbe portare a programmare manutenzioni potenzialmente non necessarie, con conseguente aumento dei costi propri di manutenzione. L’altro rischio intrinseco è di aumentare la probabilità di alcuni guasti per effetto di interventi preventivi non eseguiti correttamente.
3. Manutenzione predittiva
La manutenzione predittiva è la più recente in termini cronologici, sia a causa delle nuove esigenze nate con il progressivo sviluppo tecnologico e organizzativo dei sistemi produttivi, sia grazie alle nuove tecnologie di monitoraggio che nel tempo si sono rese disponibili. La manutenzione predittiva “è la manutenzione compiuta in risposta al degrado misurato di un’entità, cioè in base alla condizione dell’entità.” [1] Il punto focale di questo tipo di manutenzione è che se le condizioni operative dell’entità restano stazionarie e non raggiungono il livello di allerta non viene effettuato alcun intervento manutentivo. La manutenzione predittiva su condizione necessita di monitoraggio dei componenti da parte degli operatori stessi e da parte di personale addetto. Le ispezioni possono essere sensoriali (quindi visive o uditive) da parte degli addetti all’esercizio, strumentali da parte di personale addetto alle ispezioni periodiche, oppure possono essere effettuate delle ispezioni tramite test specialistici (prove non distruttive). Esistono tre modelli organizzativi per la manutenzione ispettiva: sistema accentrato, decentrato o basato sull’automanutenzione.
Manutenzione predittiva: prerequisiti
Tra i prerequisiti necessari per adottare questa politica manutentiva vi è sicuramente l’adeguata qualificazione del personale rispetto alle attività di controllo che andrà a svolgere che, oltre alle competenze specialistiche, deve possedere anche conoscenze di tipo sistemico sul processo. Un altro aspetto fondamentale è la responsabilizzazione del personale di esercizio: è necessario che l’operatore sia cosciente del ruolo fondamentale che ricopre ai fini manutentivi e al contempo è fondamentale che raggiunga la giusta sensibilità in modo da evitare segnalazioni inutili. Dal punto di vista tecnico è necessario, già in fase di progettazione, un focus preventivo sulle entità che dovranno essere manutenute e i sintomi del loro degrado. Occorrerebbe, inoltre, organizzare una verifica e taratura periodica sulla stessa attrezzatura necessaria al controllo e alle diagnosi. Una forte spinta verso questo tipo di manutenzione, in tempi molto recenti, arriva dal fenomeno dell’Industria 4.0, in particolare, dalla possibilità di integrare sistemi in grado di raccogliere e trasmettere enormi quantità di dati (IoT) e da alcuni particolari algoritmi di Machine Learning in grado di ricercare e individuare errori o anomalie nei parametri di funzionamento. Sebbene per la piena maturità tecnologica e l’impiego diffuso nelle aziende manifatturiere saranno necessari un po’ di anni, le potenzialità di queste tecnologie, anche nell’ambito della manutenzione, sono enormi.
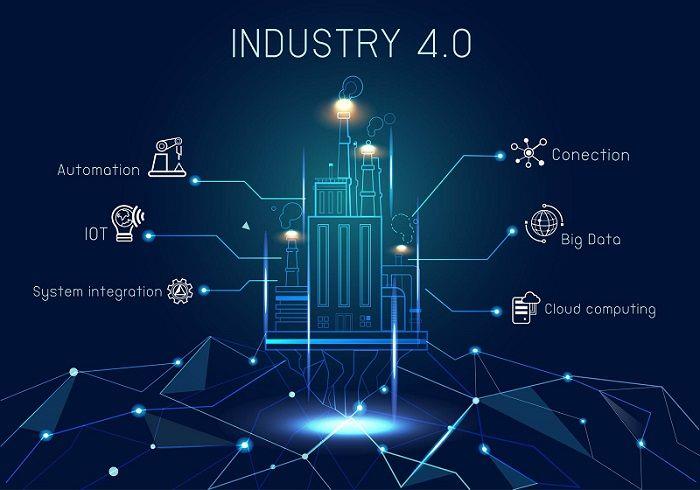
Manutenzione predittiva: vantaggi e svantaggi
Questo tipo di manutenzione permette di aumentare la disponibilità e la sicurezza dei macchinari, di raggiungere un miglior controllo sulla attività di manutenzione ed una sua maggiore qualità, giungere ad una migliore gestione del personale e, non ultimo, permette di accumulare conoscenze manutentive capitalizzabili in futuro nella progettazione di nuove entità/impianti. È importante, comunque, non sottovalutare l’investimento necessario, sia in termini di costi dovuti all’acquisto della strumentazione e alla formazione degli operatori, sia di tempo necessario allo sviluppo di una conoscenza sufficiente a mettere in atto questo tipo di manutenzione. Per questo motivo, fatto salvo i casi in cui tali attività di manutenzione vengano esternalizzate a fornitori di servizi, si preferisce dare a queste attività la forma di servizi centralizzati: in questo modo si potranno raggiungere più facilmente condizioni sufficienti a garantire il servizio condiviso su più siti di produzione.
La scelta delle politiche di manutenzione
“La scelta delle politiche di manutenzione è orientata a determinare il giusto mix di politiche di manutenzione da assegnare alle responsabilità organizzative e alle risorse disponibili.” [1] Innanzitutto, occorre tenere presente che quando i beni sono numerosi e tecnologicamente diversi fra loro, occorre stabilire le diverse politiche di manutenzione che possono essere più appropriate per ciascuna categoria di entità. In questa scelta è necessario tener conto di alcuni fattori rilevanti, come ad esempio l’impatto del guasto – valutato in termini di sicurezza, rischio ambientale, incidenza sulla qualità del prodotto/servizio, costi di mancata disponibilità e costi propri di riparazione; altri fattori chiave sono l’intervallo di guasto, come misura della sua frequenza, e la prevedibilità stessa del guasto che può essere un limite tecnico all’adozione di alcune politiche. Infine, la scelta delle giuste politiche manutentive, può avere un effetto enorme sul Phisical Asset Management, l’insieme di attività coordinate attraverso le quali un’organizzazione crea valore dalla gestione degli asset fisici lungo il loro ciclo di vita.
[1] L. FURLANETTO, M. GARETTI, M. MACCHI, 2006, PRINCIPI GENERALI DI GESTIONE DELLA MANUTENZIONE, MILANO: FRANCOANGELI