La metodologia 5S nella Lean Production
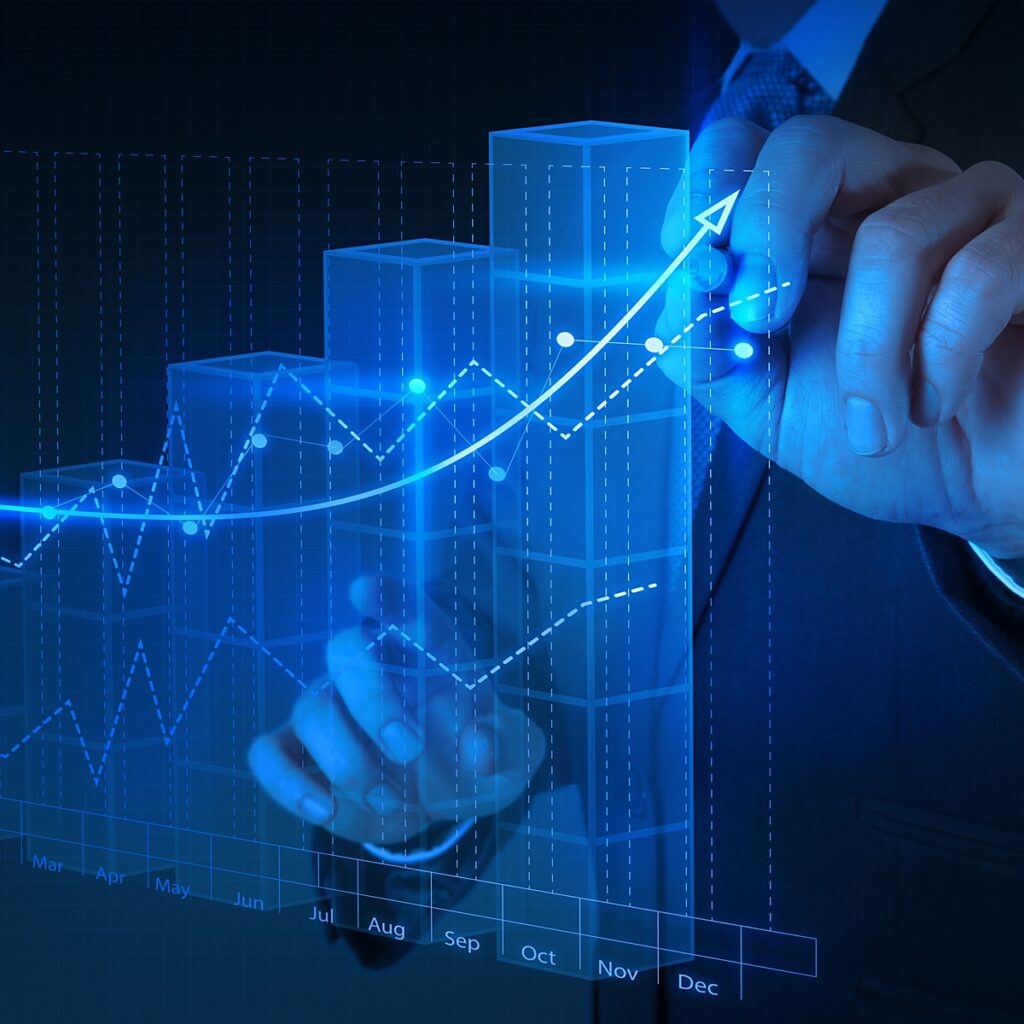
Cosa troverai in questo articolo:
Introduzione
“Metodologia 5S”: sentendo questi termini si potrebbe pensare a un qualcosa di super tecnologico e innovativo o iper complesso (forse fuorviati dal 5G o dal 5S rRNA), ma in realtà non è nulla di avulso dal mondo quotidiano. Quante volte abbiamo perso tempo a cercare ciò che ci serve? Che siano le chiavi di casa, il vestito nell’armadio, o un file nel pc… E se invece di trovarci in un contesto famigliare fossimo in un ambiente lavorativo?
In azienda le persone condividono spazi e materiali, interagiscono sulle stesse postazioni e utilizzano strumenti comuni. Cosa comporta sprecare tempo a cercare un oggetto che non ha la sua precisa collocazione? Questo:
- Incremento del Lead Time ovvero il tempo di attraversamento del prodotto o del servizio all’interno della struttura.
- Aumento dei tempi di consegna.
- Di conseguenza l’insoddisfazione del cliente.
- La probabilità di errori e inefficienze.
- Problemi di spazio
- Possibili problemi di sicurezza
Inoltre, gestire tutte queste situazioni, è un’ulteriore attività, con relativi costi.
Metodologia 5S
Il primo principio della Lean Production è identificare il valore aziendale per il cliente. Come possiamo pensare che la confusione e la disorganizzazione possano aumentare questo valore? La metodologia 5S è stata messa a punto negli anni 80′ in Toyota ed è sicuramente considerato, nell’ambito del Toyota Production System, un basic tool per avviare un processo di miglioramento continuo dell’organizzazione del lavoro.
La metodologia 5S rappresenta di fatto una guida operativa per migliorare l’ordine e la pulizia del posto di lavoro introducendo anche tecniche di gestione a vista (visual management).
I primi tre pilastri della metodologia 5S
Il termine metodologia 5S trae spunto dalle iniziali della pronuncia occidentalizzata delle cinque parole giapponesi che sintetizzano i cinque passi che danno il ritmo alla metodologia stessa:
- Seiri – separare: separa ciò che ti serve da ciò che non è funzionale all’attività e quindi crea disturbo e disordine. In pratica, la prima cosa da fare è osservare cosa c’è nell’area e definire cosa può davvero tornarci utile. La sfida, quindi, consiste nel distinguere ciò che è essenziale da ciò che non lo è. E’ importante prendersi il giusto tempo per queste operazioni; si può, per esempio, mettere un bollino rosso su quegli oggetti/documenti che si pensa possano essere eliminati, e darsi una scadenza entro la quale deciderne il destino definitivo.
- Seiton – riordinare: metti a posto tutto quello che è utile, il vecchio motto “ogni cosa al suo posto e un posto per ogni cosa”; una volta eliminato ciò che non serve, occorre sistemare in modo funzionale ciò che abbiamo conservato. Diventa importante ottimizzare l’uso dello spazio, definire in modo appropriato e facile la collocazione degli oggetti ed utilizzare al meglio le attrezzature fornite dall’azienda. La codifica degli oggetti e dell’area di lavoro consente una rapida lettura dello spazio ed una diminuzione significativa dei tempi di ricerca.
- Seiso – pulire: tieni tale ordine costante e pulisci, un ambiente pulito ed ordinato è un ambiente che “non nasconde” le inefficienze. Mantenere un alto standard di pulizia aiuta ad identificare segnali precoci di problemi. Occorre comprendere che la pulizia di un ambiente: è il modo più concreto per verificare, ispezionare, revisionare gli strumenti che l’azienda fornisce, che affida ai propri lavoratori e che si aspetta siano usati al meglio.
Gli ultimi due pilastri della metodologia 5S
- Seiketsu – standardizzare: definisci delle metodologie ripetitive e canonizzate da utilizzare per continuare queste attività di razionalizzazione delle risorse e degli spazi lavorativi; siccome i primi tre pilastri riguardano attività che devono essere ripetute nel tempo, allora per far sì che queste attività siano svolte con continuità occorre che diventino abitudini, una parte integrata nel lavoro quotidiano. Il livello di ordine, pulizia, sicurezza e semplicità d’uso dell’area deve essere continuamente monitorato (eventualmente mediante l’uso di check list).
- Shitsuke – sostenere: fai che questo modo di pensare ed agire sia pervasivo per tutte le attività aziendali. Non importa quanto bene siano stati applicate le prime quattro procedure, il sistema non può funzionare a lungo se non si applica anche quest’ ultima di mantenimento. Per il mantenimento delle 5S è molto importante sia l’impegno dell’azienda che quello dei dipendenti. Il quinto pilastro prevede le predisposizioni delle condizioni ottimali allo svolgimento di tutti processi del sistema 5S e una chiara dimostrazione dell’impegno dei dipendenti nel voler attuare le 5S.
Conclusioni
L’ordine e la pulizia “alla giapponese” non sono solo un modo di tenere pulito il posto di lavoro; sono una metodologia chiara e semplice per organizzare fisicamente e concettualmente l’azienda ed incrementare da subito l’efficienza senza necessariamente investire risorse economiche. Ecco perché spesso, quando si avviano progetti di Lean Production, all’interno di molte organizzazioni si comincia proprio dalla metodologia 5S.
Articolo di Matteo Cosenza